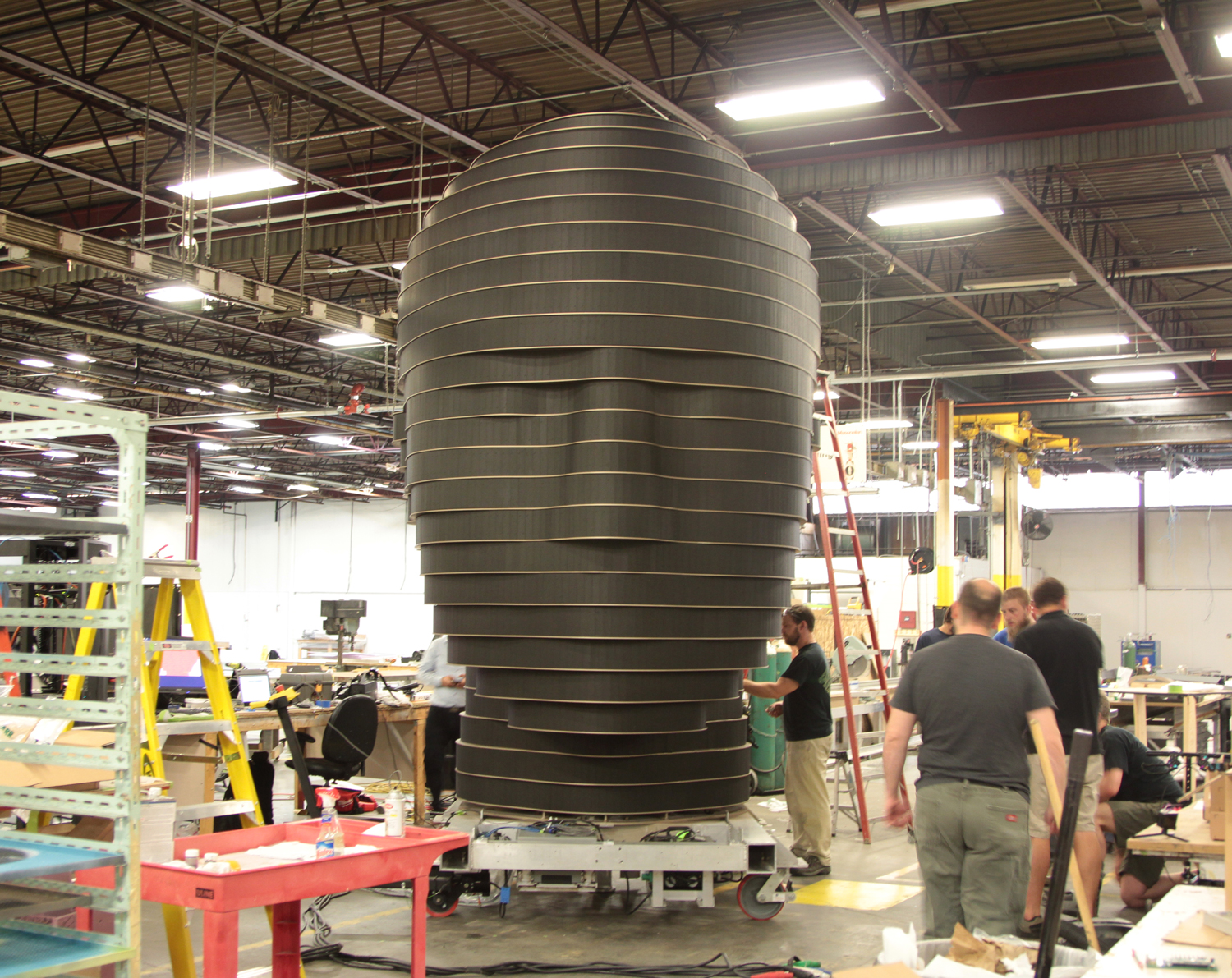
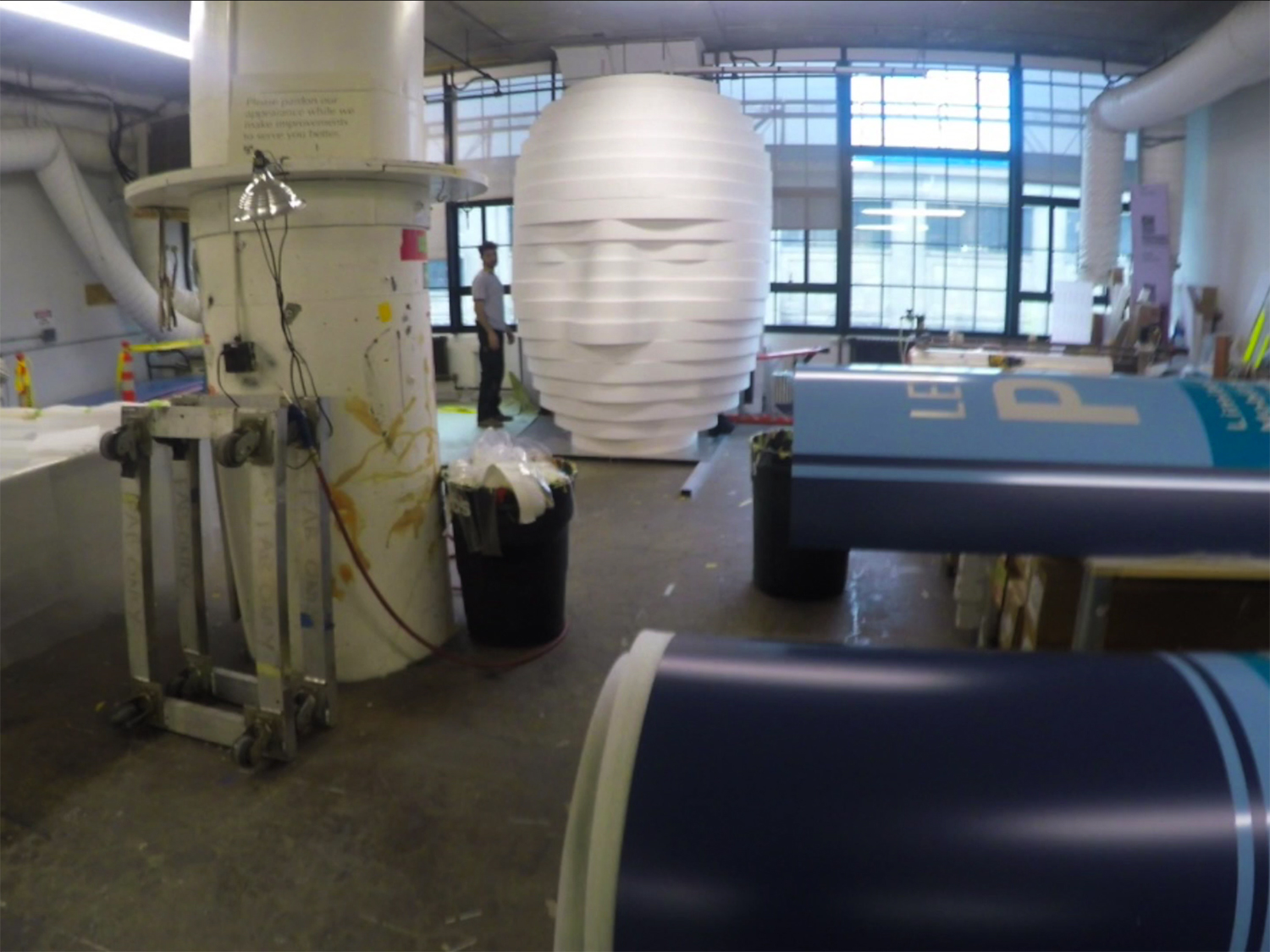
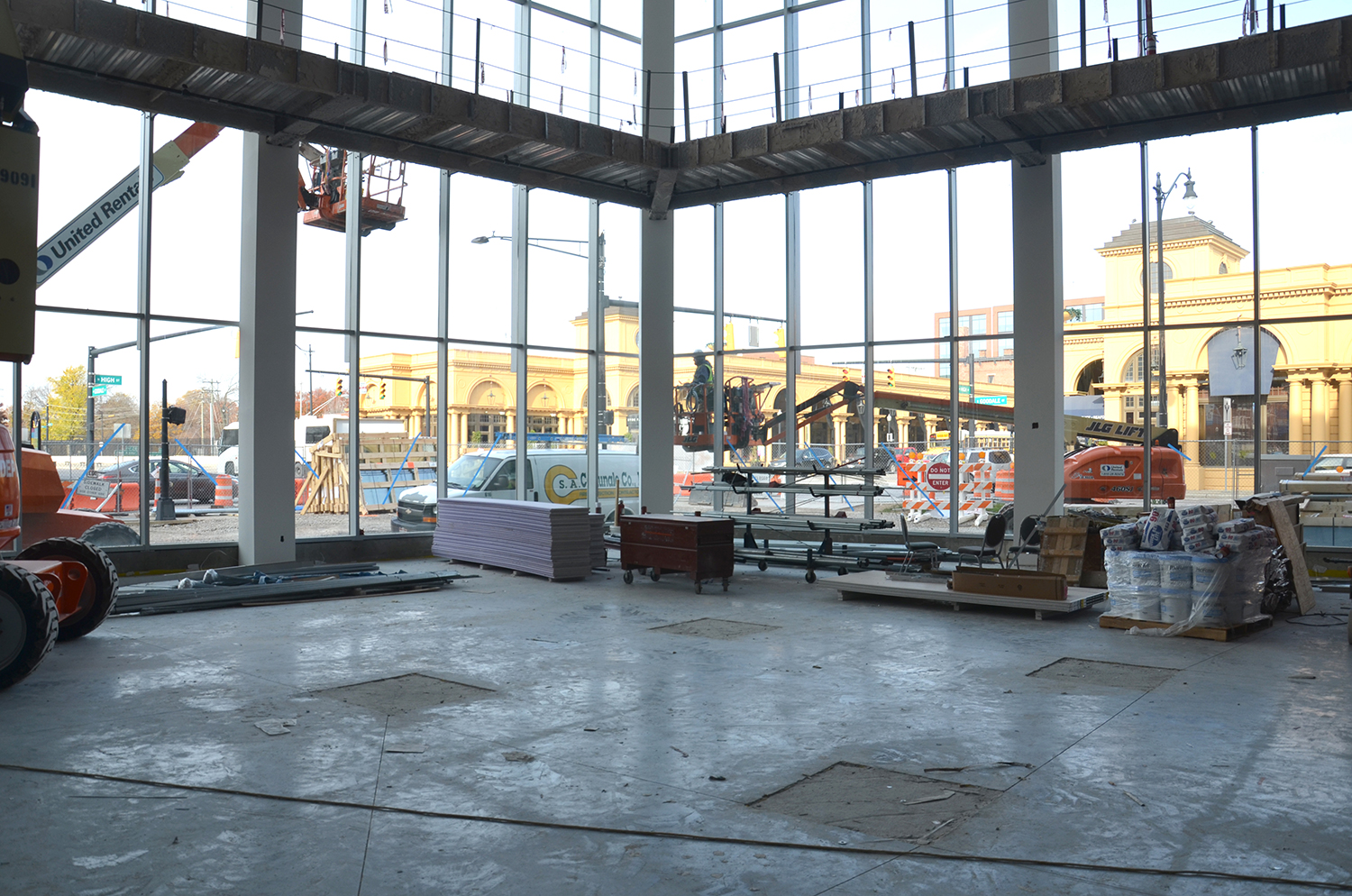
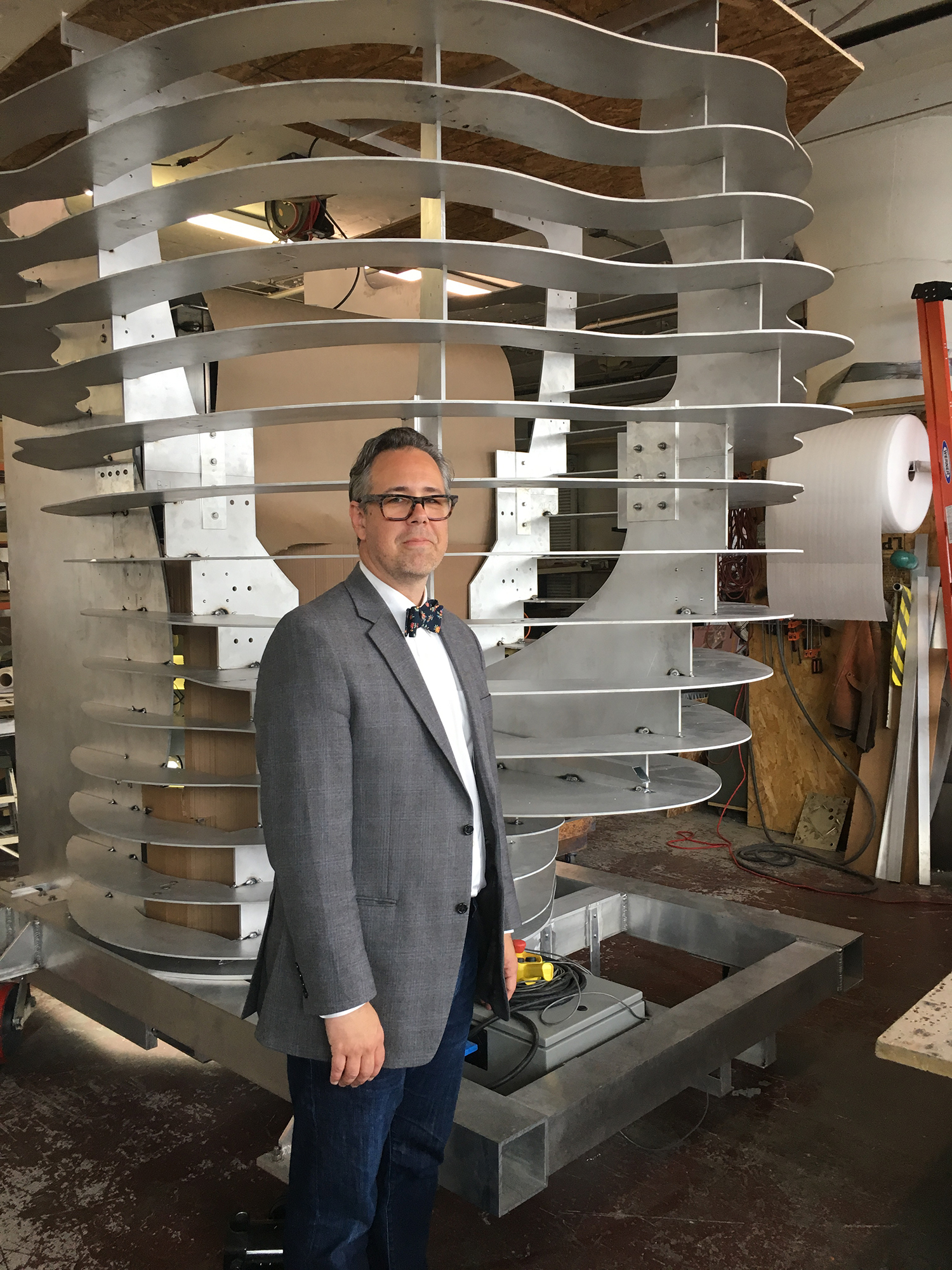
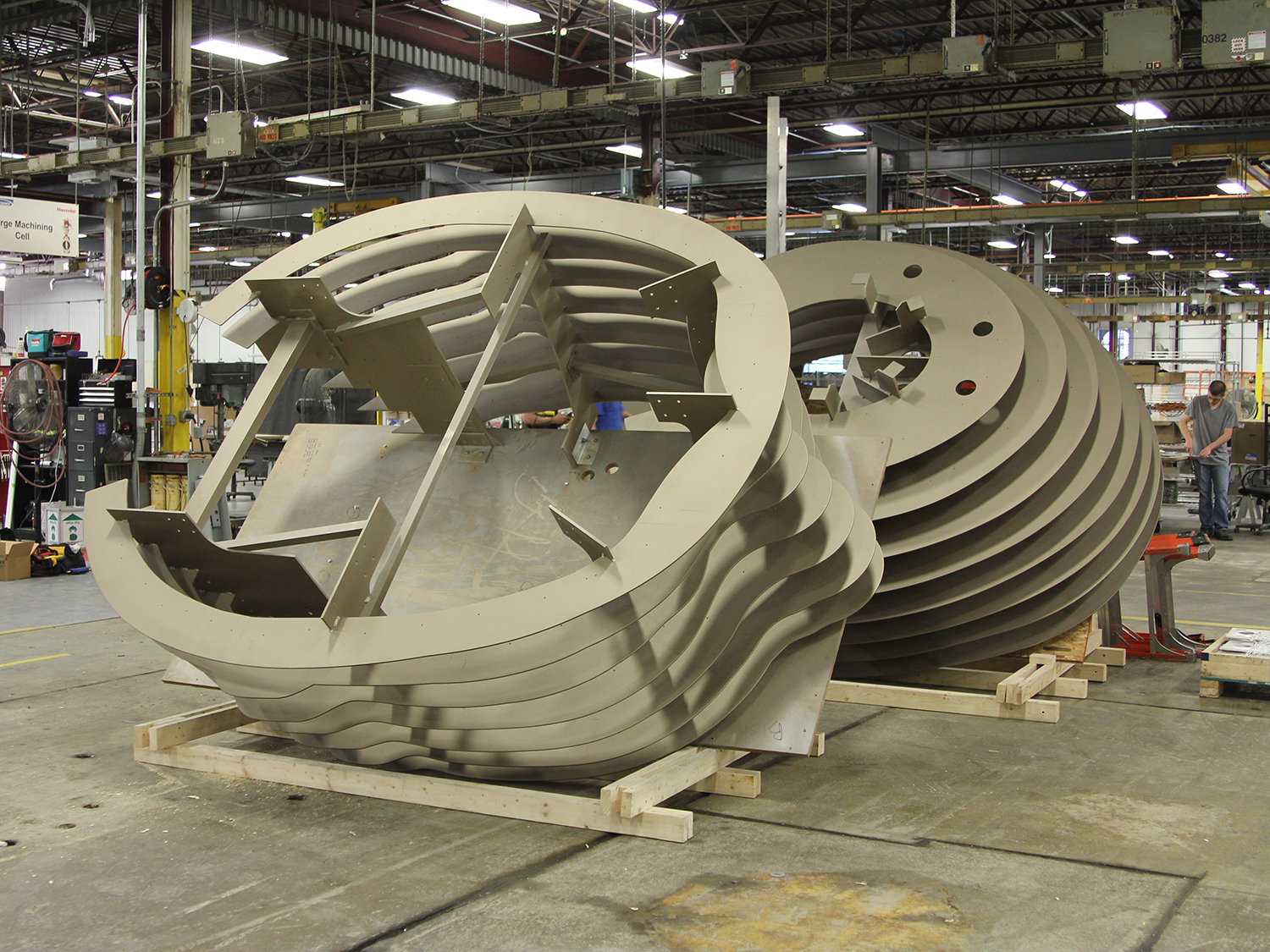

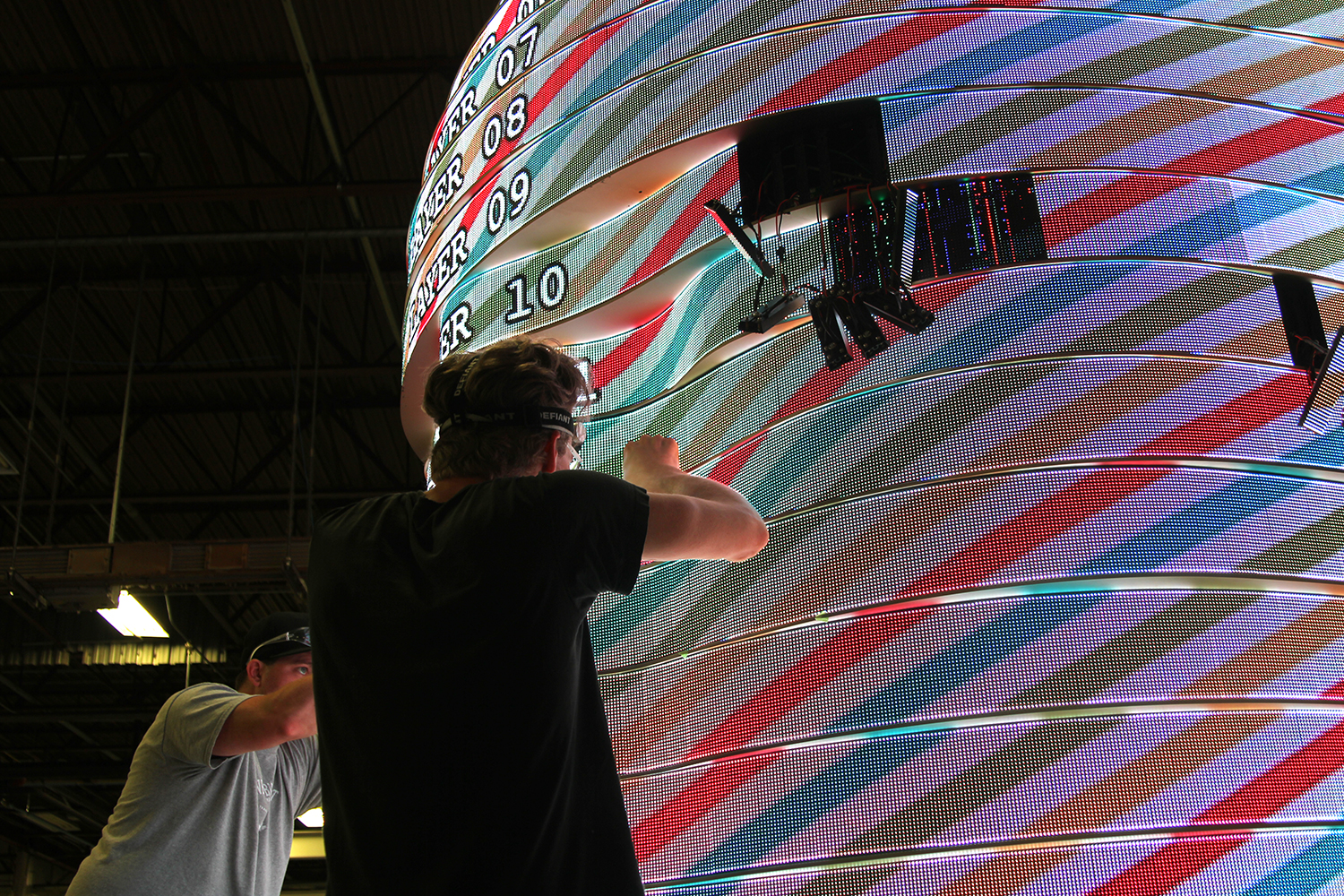
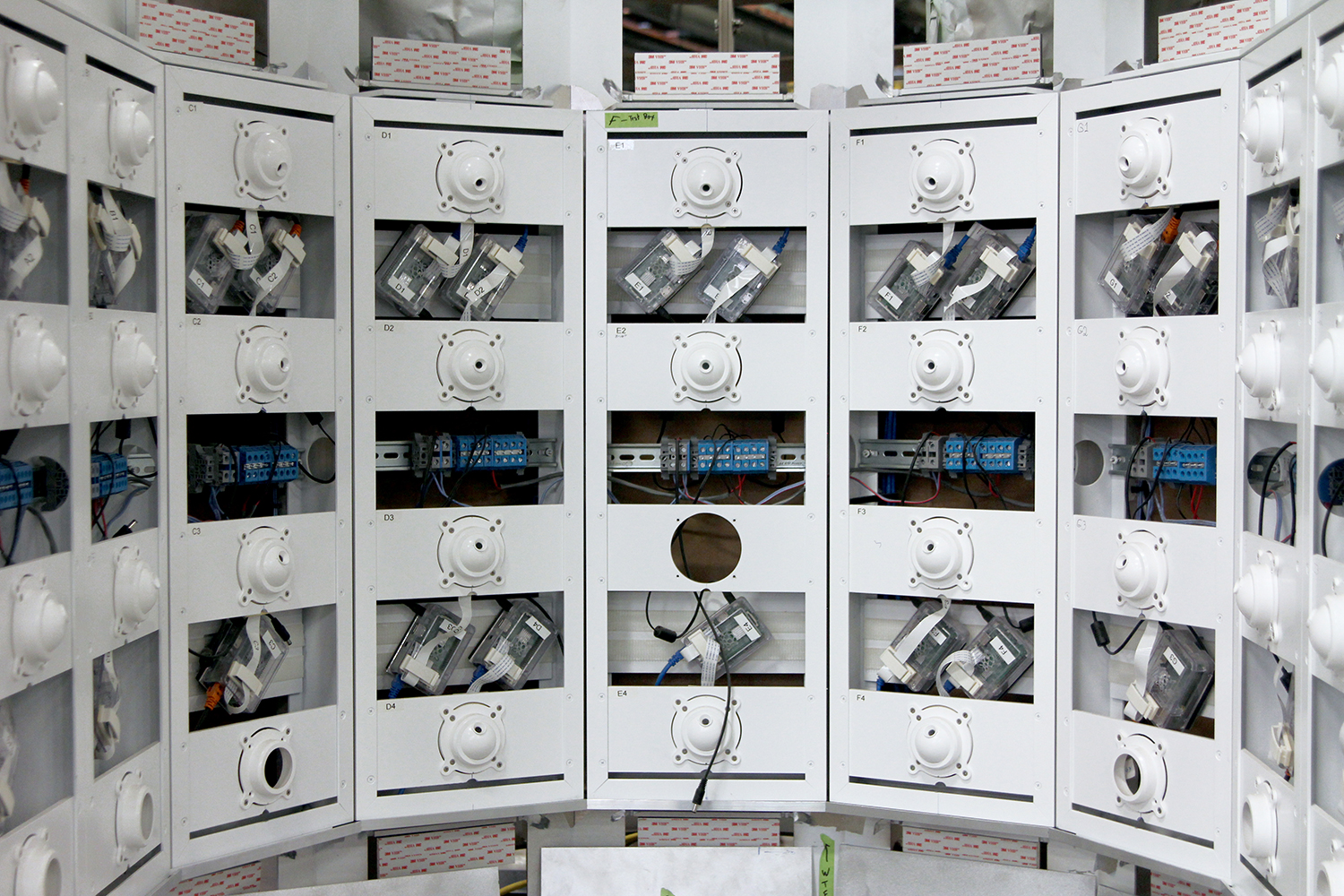
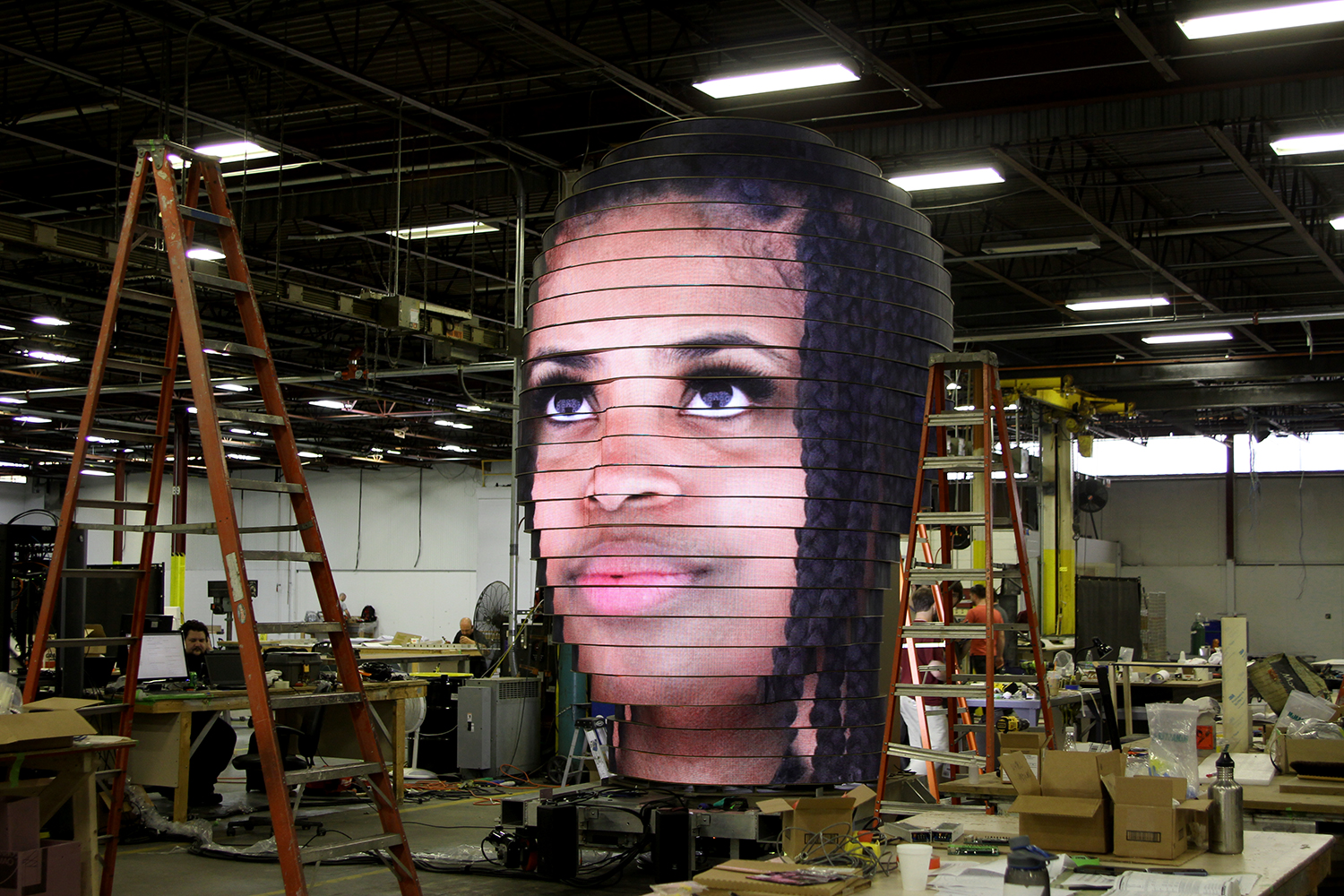
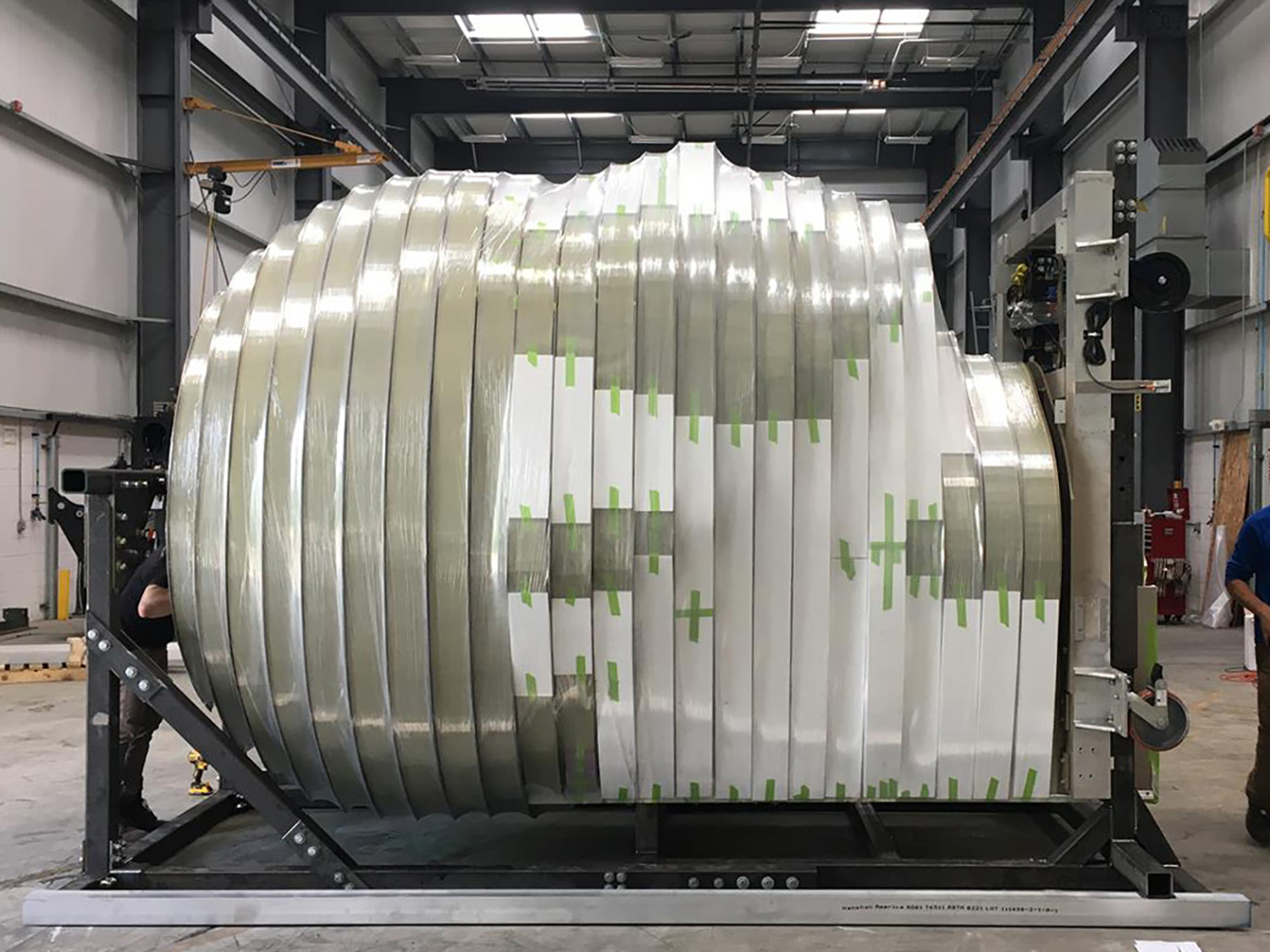
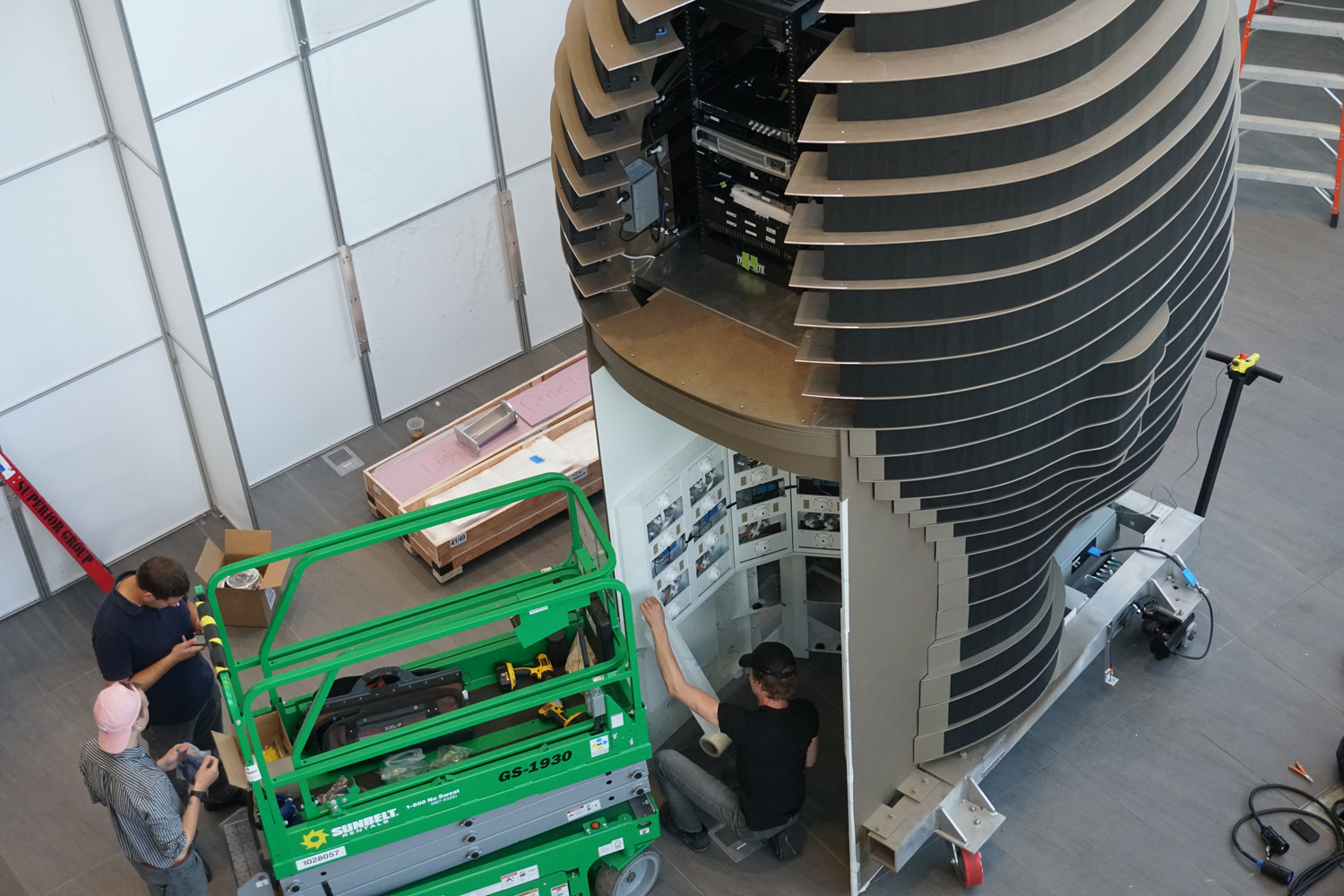
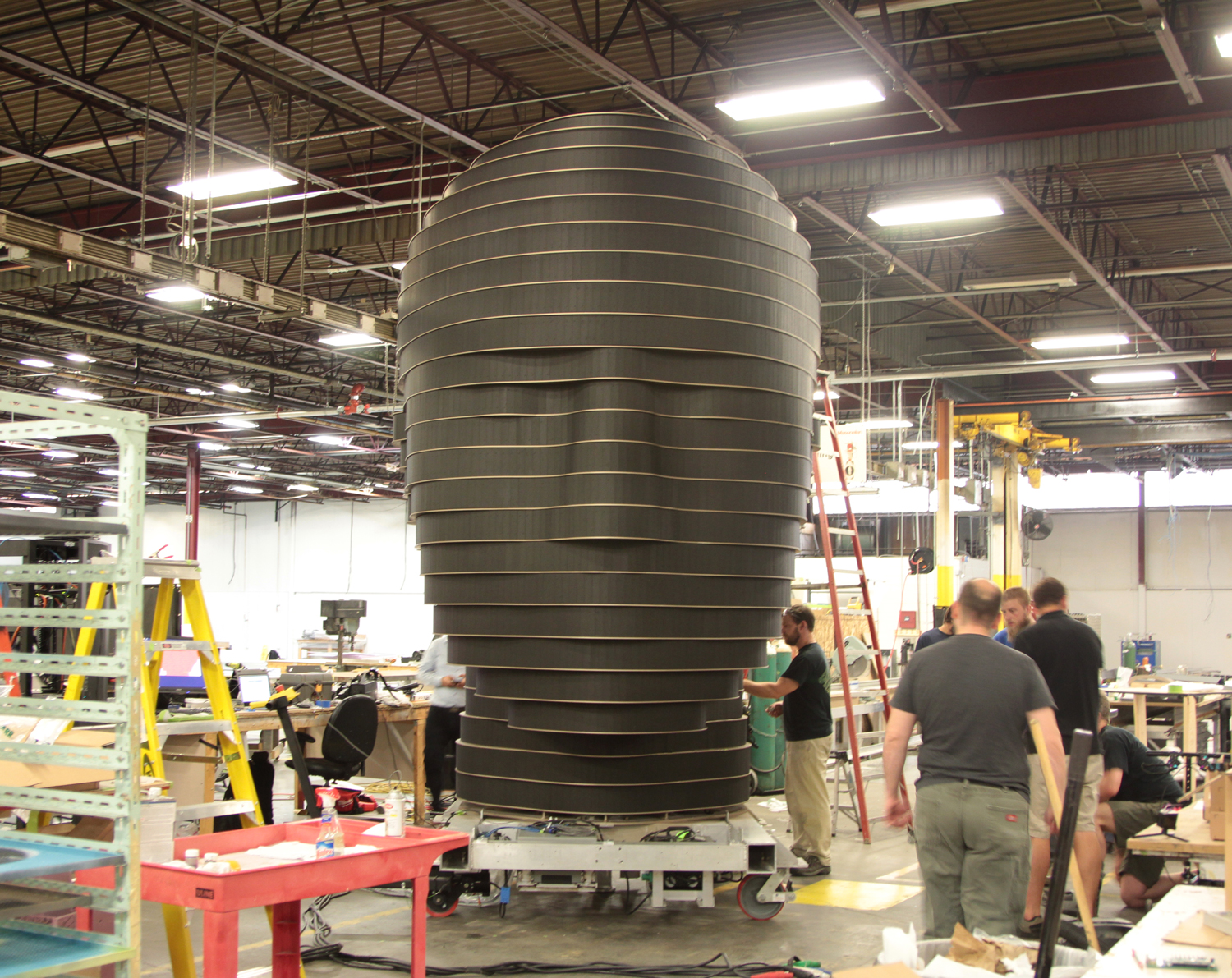
Many people see technology as a necessary evil or another appliance. When it is used in service of conceptually driven content it can become magic, especially when it leaves the screen and becomes physical interaction.
Jeff Grantz, Tom Saylor, and Mac Pierce of Design Communications Limited brought ‘As We Are’ to life, assembling a team of talented individuals andcompanies to create a first of its kind experience.
All technologies are either off the shelf or proprietary, though never before coordinated or automated as they are in the sculpture.
photo by Tom Bergeron, courtesy of DCL Boston
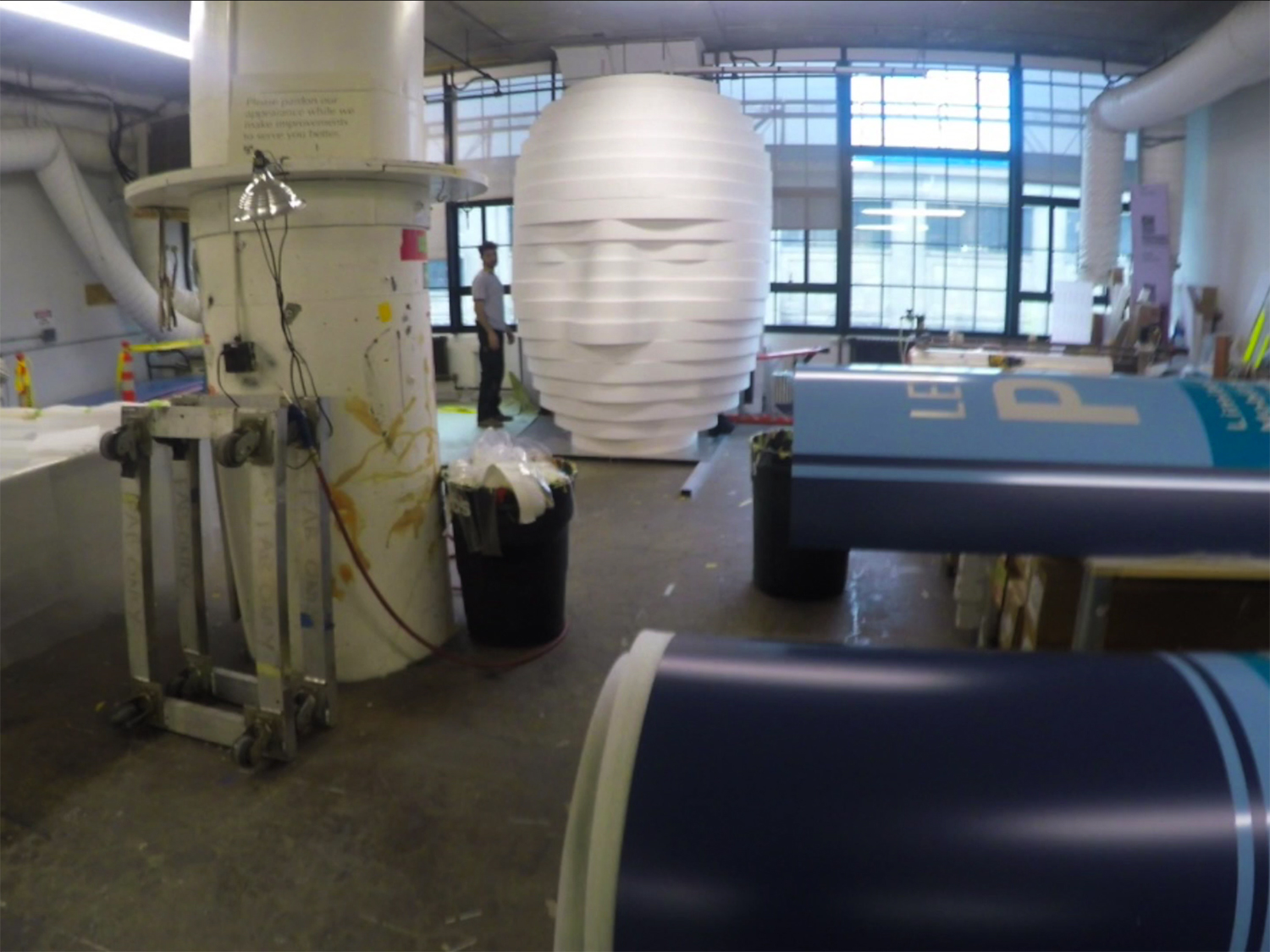
This was the prototype made from hot-wire cut foam. It was what we first saw our faces projected on as a test of scale.
My first impression was a bit terrifying. I blushed, it was uncomfortable. There were details good and bad.
After about ten or so seconds, I became at piece with it, this is how I move through the world. Short of plastic surgery, all I can do is take care of myself. My genetics are what they are and it's okay.
photo by Tom Bergeron, courtesy of DCL Boston
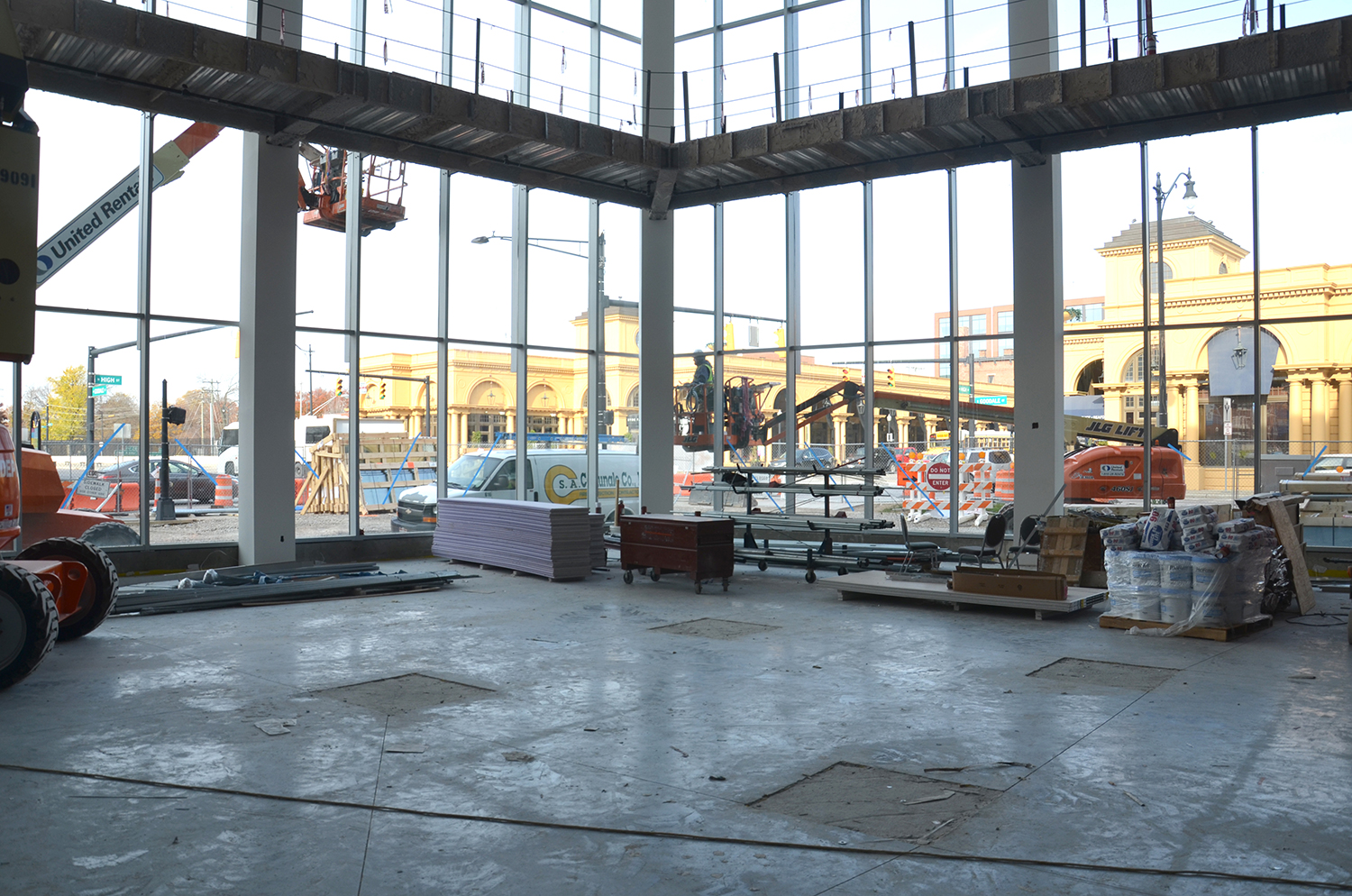
One of my favorite moments in the process was marking the floor where I wanted the sculpture to go. I did some visual measurements and used a sharpie.
The finished atrium by LMN Architects and built by Corna-Kokosing is breathtakingly beautiful. It is an honor to have my work there.
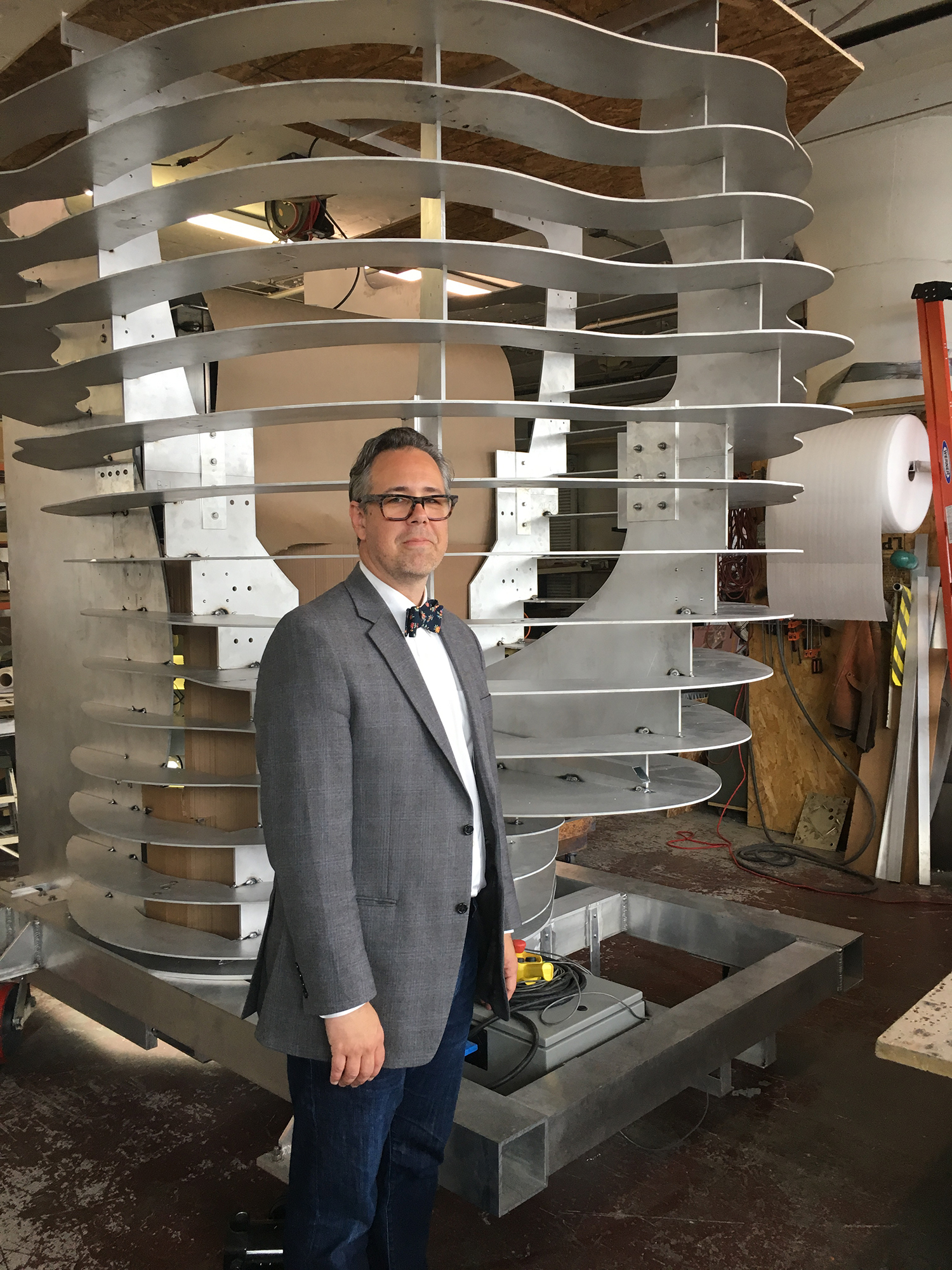
Gives a sense of the height. The chassis is shown here.
photo by Tom Bergeron, courtesy of DCL Boston
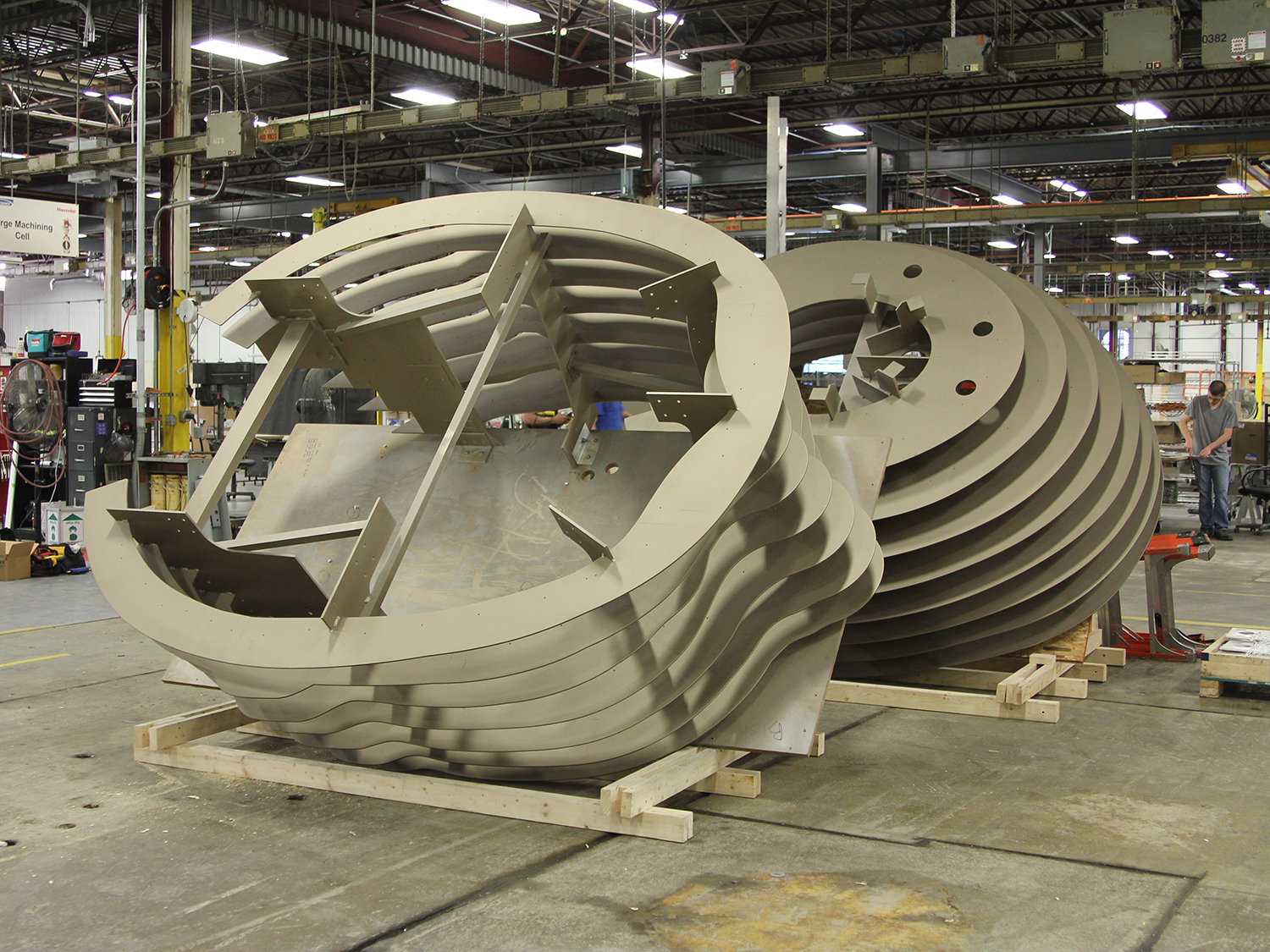
CNC cut aluminum structure. The color choice, a subtle bronze, references thousands of years of sculpture and works well with all complexions.
photo by Tom Bergeron, courtesy of DCL Boston

Finished cases of LEDs were air shipped from China. Special thanks to Sansi North America
photo by Tom Bergeron, courtesy of DCL Boston
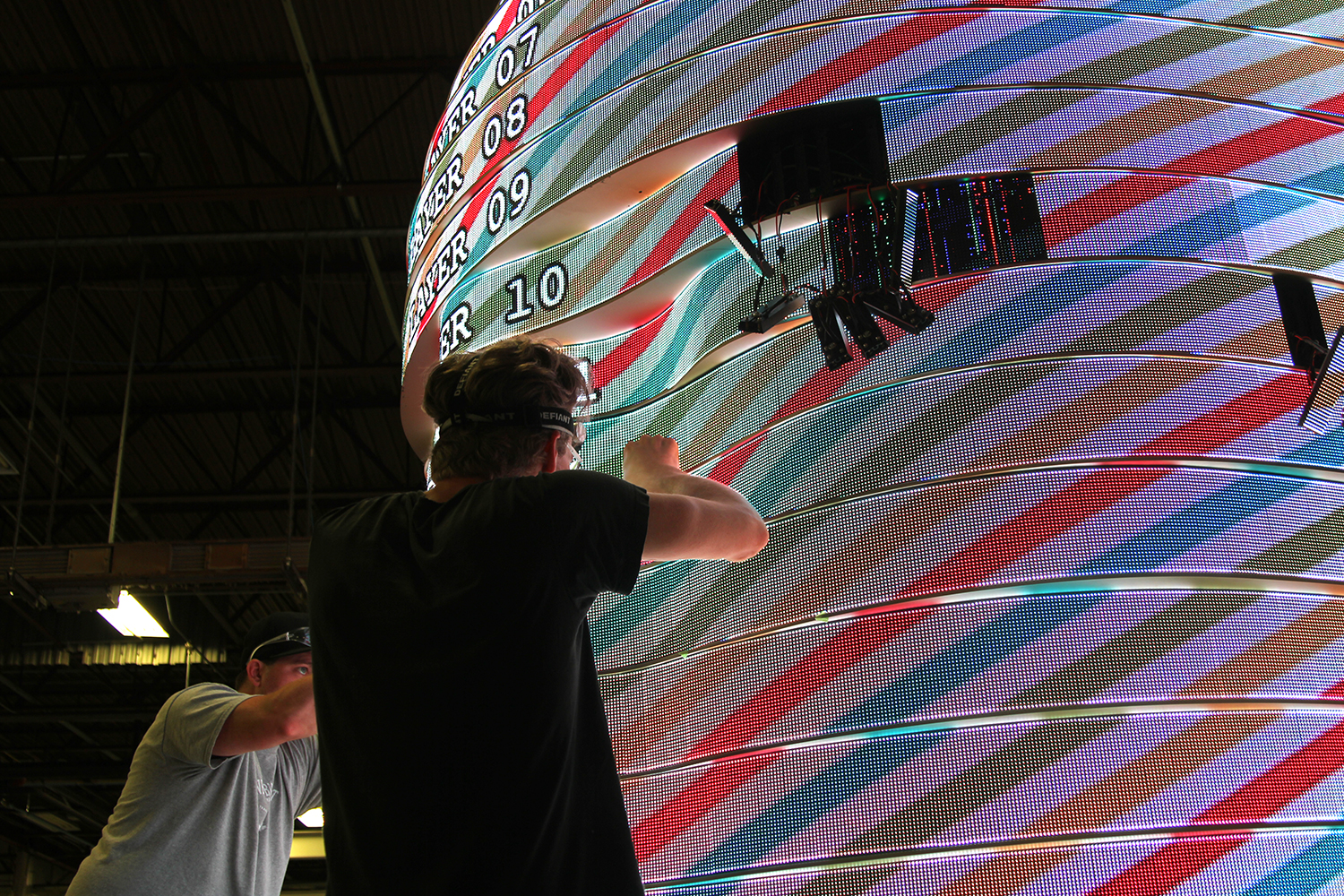
The sculpture has 3000, custom engineered LED panels for a total of over 850,00 lights. These were provided by Sansi North America.
The panels were designed to accomodate the tightest radius, the bridge of the nose.
photo by Tom Bergeron, courtesy of DCL Boston
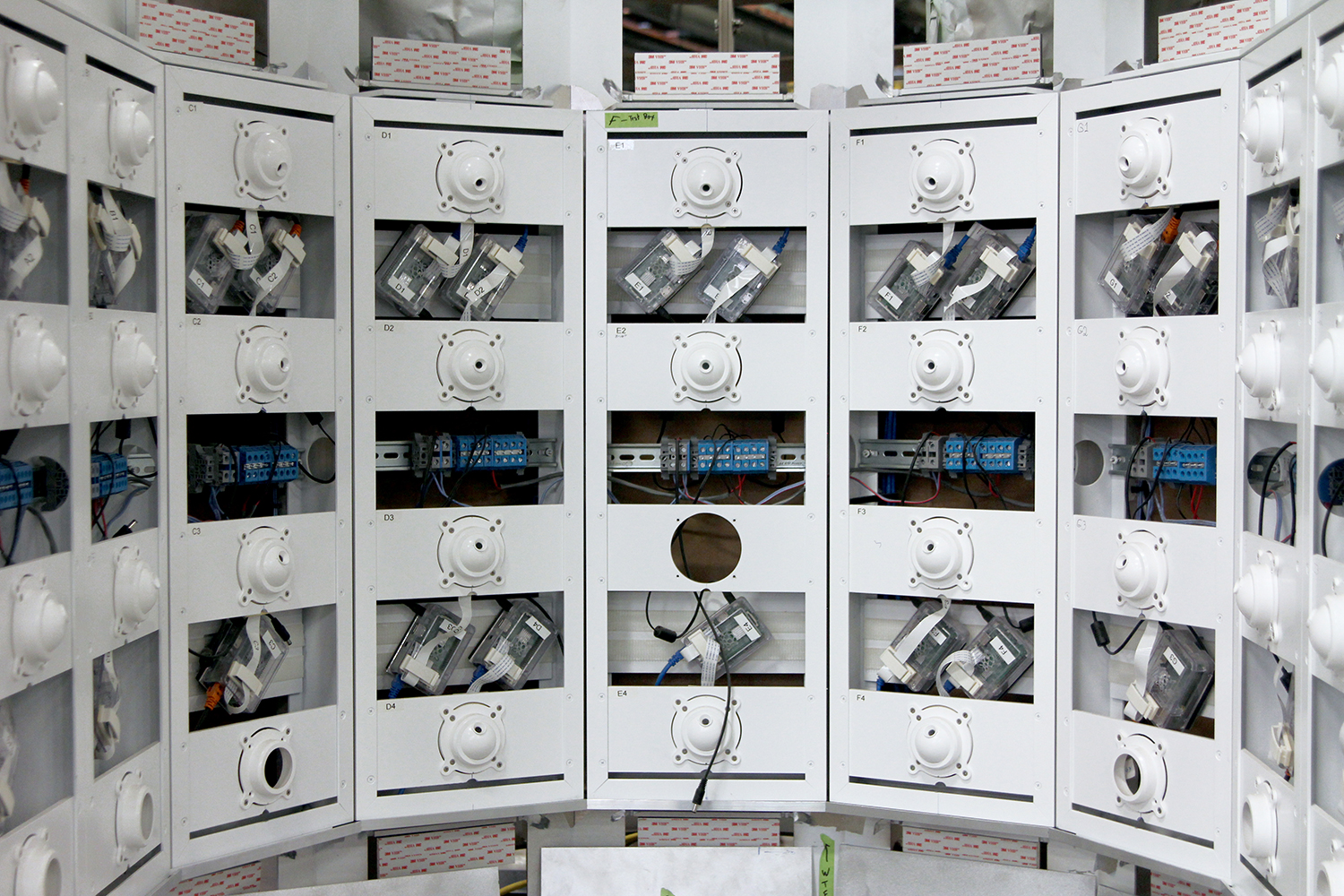
The photo booth uses a process called photogrammetry in which twenty-nine images are taken simultaneously. A 3D model of your head is generated from these photos and all images are stitched together on it.
DCL worked with a Direct Dimensions who integrated their process with Creosphere, the interface developer.
photo by Tom Bergeron, courtesy of DCL Boston
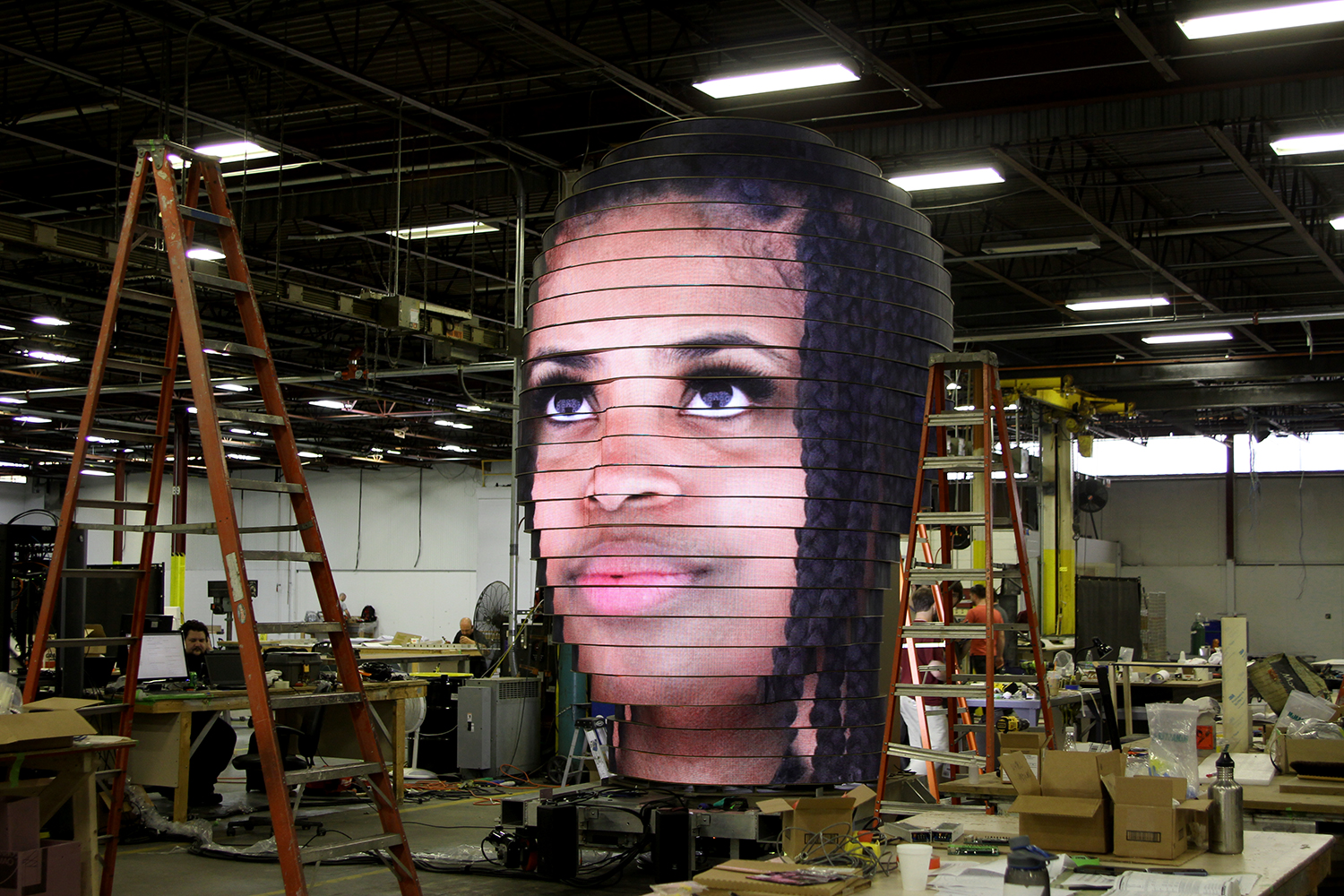
The experiences of people doing user testing ranged from delight to trepidation to preoccupation with what it means or how it works. The Project Manager had to shoo coworkers and visitors away because productivity in their shop was dropping; people would just stop and stare at the sculpture when faces were displayed on it.
photo by Tom Bergeron, courtesy of DCL Boston
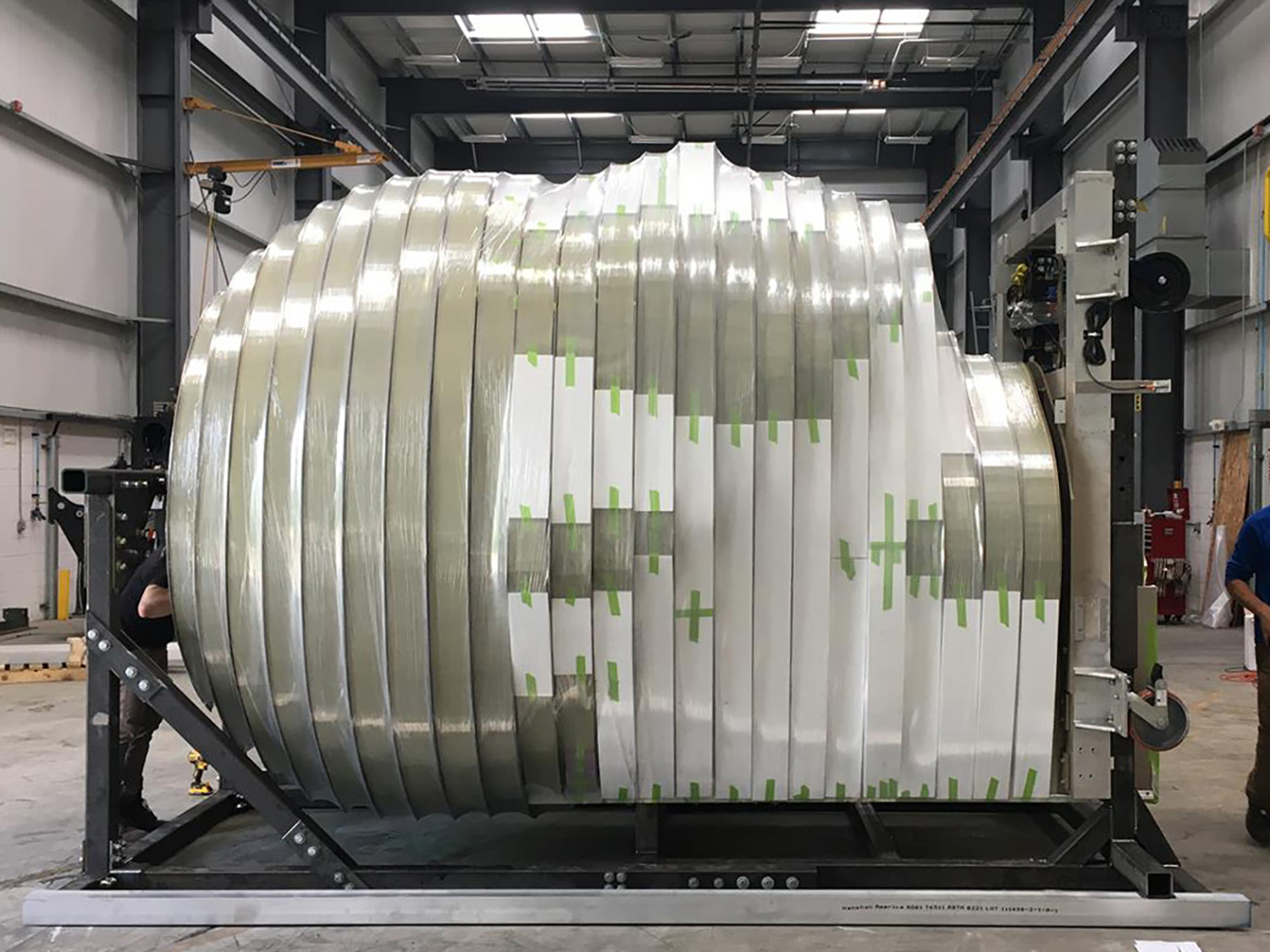
The structure was engineered with shipping in mind. A removable spine was placed inside to provide extra support for the ride from Boston to Chicago.
Tom Saylor went over the logistics with me. Every detail took into account physics, process, and what if's. It was magnificently orchestrated.
photo by Tom Bergeron, courtesy of DCL Boston
The owner of the trucking company drove the sculpture from Boston to Columbus. He said, “I would trust any of my employees to drive a forty million dollar jet engine across the country but I personally wanted to do this job.”
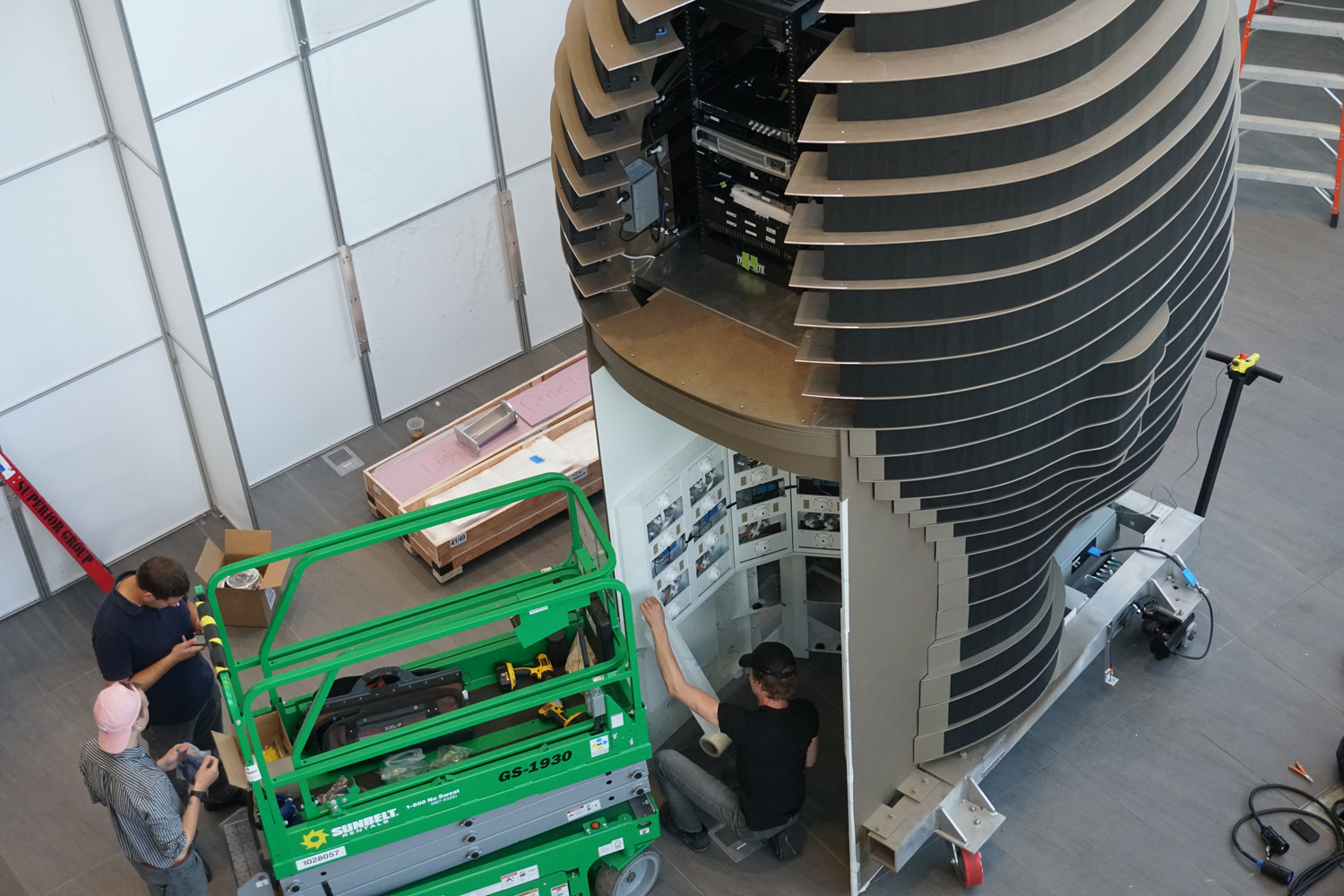
It is capable of storing 100,000 portraits on-site and all images are stored in the cloud indefinitely. No expense was spared in security or performance.
photo by Tom Bergeron, courtesy of DCL Boston